COMPANY
GREETING
For over six decades, we have specialized in a very niche yet crucial component – the manufacturing of valve plate for airconditioning compressors. The trust and reputation we have built over these years are our most significant assets.
In a time where many Japanese companies are facing challenges in the global market, our growth at Kashima Seiki Industrial can be attributed to the vision and indomitable spirit of our past presidents. This is further bolstered by our strategic achievements, including:
・Successfully localizing our business overseas (managed by local professionals) ensuring prompt support for our customers globally.
・A relentless pursuit of innovative technologies to enhance quality.
・An unwavering dedication to always prioritizing our customers.
Today, Kashima Seiki Industrial is renowned both in Japan and globally for our commitment to quality and timely delivery. We believe, however, that there is no room for complacency. Guided by our mission to “”Support global development through manufacturing,”” we are more committed than ever to broaden our sincere efforts across the world. We are dedicated to addressing and solving the various challenges faced by the manufacturing industry.
Our principle of “”customer first”” remains at the forefront of our operations, irrespective of our organizational growth. Our goal is to continually be the best manufacturing partner for our customers.
To all our valued customers, we promise our continued commitment to delivering satisfaction beyond your expectations.
We thank you for your continued support and trust for Kashima Seiki.
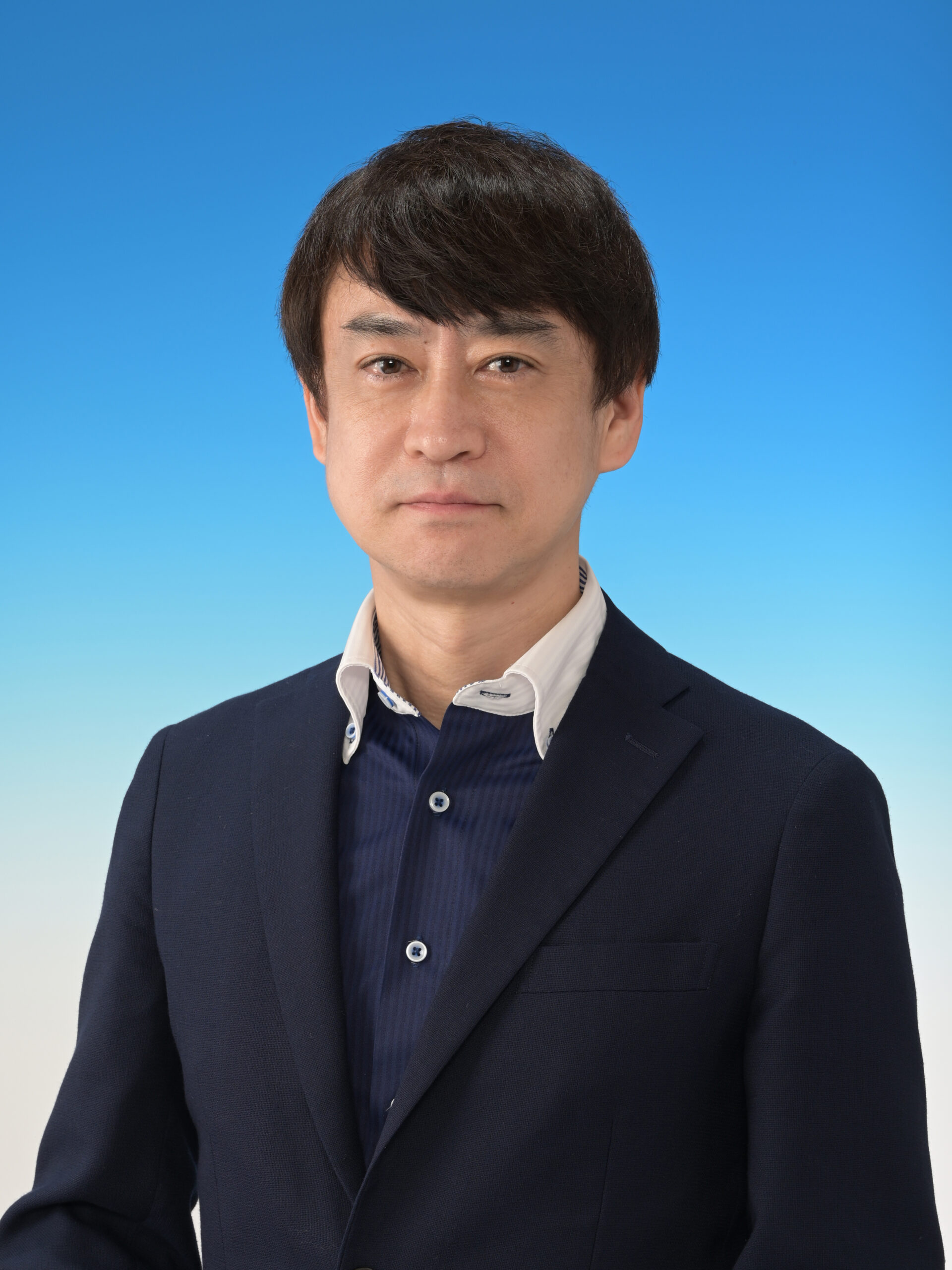
Yu Nakajima
President and CEO
Kashima Seiki Industrial
PHILOSOPHY
【MISSION】
・Support the global development through manufacturing
【VISION】
・Lead the world manufacturing with quality and criativity
・Challenge difficulties with innovative technology
【VALUE】
・Always challenging with new technologies
・Adapt to the changing world
・Make the impossible possible with creative ideas
PHILOSOPHY
【MISSION】
・Support the global development through manufacturing
【VISION】
・Lead the world manufacturing with quality and criativity
・Challenge difficulties with innovative technology
【VALUE】
・Always challenging with new technologies
・Adapt to the changing world
・Make the impossible possible with creative ideas
COMPANY PROFILE
COMPANY | Kashima Seiki Industrial Co.,Ltd. |
---|---|
Founded | December 6th, 1962 |
Location | 574-2 Kozu, Nagao-cho, Kita-ku, Kobe-shi, Hyogo, Japan, 651-1512 |
Capital | 10 million yen |
Number of Employees | 150(consolidated) |
Management | CEO Yu Nakajima |
TEL | +8178-986-2368 |
FAX | +8178-986-2368 |
kashima@kashimaseiki.com | |
Sales | 2 billion yen(consolidated) |
Main Clients | Compressor for Air Conditioners and Refridgerators/Freezers, Precision Instruments, Cameras, etc. |
Main Bank | Sumitomo Mitsui Banking Corporation |
HISTORY
Kashima Seiki Co., Ltd is founded at Kohama, Takarazuka.
Sanda Plant is established.
Kita-Kobe Plant is established.
Kashima(Malaysia) Sdn. Bnd. is established.
Kashima Precision Machining is established.
Nagano Plant is established.
P.T.Kashima Seiki Indonesia is established.
Guangzhou Nansha(広州南沙)Kashima is established.(Closed now)
Head office is transferred to Kita-Kobe Plant.
Jiangmen(江門) Kashima was established.
PLANT
・Kita-Kobe Plant
574-2 Kozu, Nagao-cho, Kita-ku, Kobe-shi, Hyogo, Japan, 651-1512
Kita-Kobe Plant
■Barrel Finishing Process
The plant has 31 rotary barrel finishing machines, which can polish and finish a large amount of products in one lot. There are also 6 centrifugal barrel finishing machines for small lots or small parts (3mm to 5mm square). We specialize in polishing thin plates such as valve plates for air conditioner compressors and pressure switches for automobiles.
Kita-Kobe Plant
・Kita-Kobe Plant
574-2 Kozu, Nagao-cho, Kita-ku, Kobe-shi, Hyogo, Japan, 651-1512
■Barrel Finishing Process
The plant has 31 rotary barrel finishing machines, which can polish and finish a large amount of products in one lot. There are also 6 centrifugal barrel finishing machines for small lots or small parts (3mm to 5mm square). We specialize in polishing thin plates such as valve plates for air conditioner compressors and pressure switches for automobiles.
Sanda Plant
■Precision Stamping Process
We specialize in the processing of thin plates used in pressure switches for automobiles. Since pressure switches are opened and closed at a specific pressure, they are extremely delicate products. The molding and adjustment are performed by highly skilled workers.
・Sanda Plant
39-2 Kono, Sanda-shi, Hyogo, Japan, 669-1331
Sanda Plant
・Sanda Plant
39-2 Kono, Sanda-shi, Hyogo, Japan, 669-1331
■Precision Stamping Process
We specialize in the processing of thin plates used in pressure switches for automobiles. Since pressure switches are opened and closed at a specific pressure, they are extremely delicate products. The molding and adjustment are performed by highly skilled workers.
・Nagano Plant
5268-219 Hosono, Matsukawa-mura, Kita-Azumino-gun, Nagano, Japan, 399-8501
Nagano Plant
■Precision Stamping Process
The plant has 25- to 110-ton press machines and specializes in the forming and pressing of thin plates with thicknesses ranging from 0.05 mm to 5 mm. We have a long track record in the production of valve plates for air conditioner compressors and pressure switches for automobiles.
■Mold Design and Fabrication Process
We design molds to meet high-quality requirements and provide various types of products for more than 30 years.
Nagano Plant
・Nagano Plant
5268-219 Hosono, Matsukawa-mura, Kita-Azumino-gun, Nagano, Japan, 399-8501
■Precision Stamping Process
The plant has 25- to 110-ton press machines and specializes in the forming and pressing of thin plates with thicknesses ranging from 0.05 mm to 5 mm. We have a long track record in the production of valve plates for air conditioner compressors and pressure switches for automobiles.
■Mold Design and Fabrication Process
We design molds to meet high-quality requirements and provide various types of products for more than 30 years.
China Plant
■Precision Stamping Process
Products are pressed in a single progressive stamping process, and any chips or other defects on the product surface are effectively controlled. Sampling is conducted following strict inspection standards to minimize the defects of products. More over, regular mold maintenance is performed.
■Barrel Finishing Process
The rotary barrel process improves the fatigue strength of products at when performed with adequate time and selected media(grinding stones)to form residual compressive stresses. Utilizing superior abrasives effectively assures the surface smoothness of products. Polishing effectively removes fine burrs on the side of the product and the cross-sectional shape will be round and smooth.
・China Plant
GUANGDONG PROVINCE,JIANMEN CITY,HESHAN CITY,GONGHE TOWN,XINCAILIAO JIDI(NEW MATERIAL BASE)No,21-8
China Plant
・China Plant
GUANGDONG PROVINCE,JIANMEN CITY,HESHAN CITY,GONGHE TOWN,XINCAILIAO JIDI(NEW MATERIAL BASE)No,21-8
■Precision Stamping Process
Products are pressed in a single progressive stamping process, and any chips or other defects on the product surface are effectively controlled. Sampling is conducted following strict inspection standards to minimize the defects of products. More over, regular mold maintenance is performed.
■Barrel Finishing Process
The rotary barrel process improves the fatigue strength of products at when performed with adequate time and selected media(grinding stones)to form residual compressive stresses. Utilizing superior abrasives effectively assures the surface smoothness of products. Polishing effectively removes fine burrs on the side of the product and the cross-sectional shape will be round and smooth.
・Malaysia Plant
Jalan P/15, Seksyen 10, Kawasan Perindustrian MIEL, Fasa IV, Bandar Baru Bangi, 43650, Bangi, Selangor, 43650 Malaysia
Malaysia Plant
■Precision Stamping Process
We have 10- to 150-ton press machines and specialize in compressor valves for automobiles and air conditioners. Equipped with a wide range of pressing capacities, we are able to supply any kinds of products with required quality by arranging materials from Malaysia, Japan, Taiwan, China, Sweden, and other countries. We can handle plate thicknesses in the range from 0.152 mm to 4.0 mm, and can also supply customers in Japan and other countries by integrated processing from die arrangements (progressive and single-shot) to deburring and heat treatment, etc.
■Barrel Finishing Process
Since we have 37 rotary barrel machines, 7 centrifugal barrel machines, vibratory barrel machines, and a large number of abrasives, we are capable of processing large quantities under specified conditions with short delivery times. The plant is also equipped with a water purification facility, which complies with government regulations, and is operated environmentally friendly.
Malaysia Plant
・Malaysia Plant
Jalan P/15, Seksyen 10, Kawasan Perindustrian MIEL, Fasa IV, Bandar Baru Bangi, 43650, Bangi, Selangor, 43650 Malaysia
■Precision Stamping Process
We have 10- to 150-ton press machines and specialize in compressor valves for automobiles and air conditioners. Equipped with a wide range of pressing capacities, we are able to supply any kinds of products with required quality by arranging materials from Malaysia, Japan, Taiwan, China, Sweden, and other countries. We can handle plate thicknesses in the range from 0.152 mm to 4.0 mm, and can also supply customers in Japan and other countries by integrated processing from die arrangements (progressive and single-shot) to deburring and heat treatment, etc.
■Barrel Finishing Process
Since we have 37 rotary barrel machines, 7 centrifugal barrel machines, vibratory barrel machines, and a large number of abrasives, we are capable of processing large quantities under specified conditions with short delivery times. The plant is also equipped with a water purification facility, which complies with government regulations, and is operated environmentally friendly.
Indonesia Plant
■Precision Stamping Process
We have 35- to 80-ton press machines and specialize in stamping metal sheets (more than 0.10 mm thinness) mainly for motorcycles and automobiles. We can provide integrated processing from die design (progressive or single-shot) to deburring. We can supply materials from Japan, Taiwan, China, Sweden, and other countries, and we also supply to customers outside Indonesia. We can also arrange gasket materials, design molds (one-shot), and process products.
■Barrel Finishing Process
We have 12 rotary barrel machines, vibrating barrel machines, eddy current barrel machines, and a large selection of abrasives, which enables us to provide the same quality and processing conditions as in Japan. We have good reputation for small-lot production and can perform luster polishing, degreasing, and rustproofing treatments if required.
■Spring / Coiling Process
We produce compression coil springs and ring stoppers for motorcycles and appliances by processing piano wire, stainless steel wire, and various other wires (diameter from 0.5 mm to 2.0 mm). We also offer integrated processing including deburring (barrel finishing) of cross-sectional surfaces and surface polishing if required.
・Indonesia Plant
Jl. Jababeka IV, SFB BLOK T No.2-1, Pasirgombong, Kec. Cikarang Utara, Kabupaten Bekasi, Jawa Barat 17530 Indonesia
Indonesia Plant
・Indonesia Plant
Jl. Jababeka IV, SFB BLOK T No.2-1, Pasirgombong, Kec. Cikarang Utara, Kabupaten Bekasi, Jawa Barat 17530 Indonesia
■Precision Stamping Process
We have 35- to 80-ton press machines and specialize in stamping metal sheets (more than 0.10 mm thinness) mainly for motorcycles and automobiles. We can provide integrated processing from die design (progressive or single-shot) to deburring. We can supply materials from Japan, Taiwan, China, Sweden, and other countries, and we also supply to customers outside Indonesia. We can also arrange gasket materials, design molds (one-shot), and process products.
■Barrel Finishing Process
We have 12 rotary barrel machines, vibrating barrel machines, eddy current barrel machines, and a large selection of abrasives, which enables us to provide the same quality and processing conditions as in Japan. We have good reputation for small-lot production and can perform luster polishing, degreasing, and rustproofing treatments if required.
■Spring / Coiling Process
We produce compression coil springs and ring stoppers for motorcycles and appliances by processing piano wire, stainless steel wire, and various other wires (diameter from 0.5 mm to 2.0 mm). We also offer integrated processing including deburring (barrel finishing) of cross-sectional surfaces and surface polishing if required.